Плазменная резка: основные плюсы и минусы технологии
Резка металла – задачка, с которой часто сталкиваются на промышленных предприятиях, в мастерских, на строй площадках. На сегодня существует несколько методов реализации обозначенных процессов. Более обычным является внедрение автогена. Но эта разработка не всегда является действенной и оправданной. При наличии огромных объемов продукции и больших требований к качеству обработанных заготовок стоит предпочесть плазменную резку, осуществляющуюся средством специального аппарата.
1-ый плазморез был спроектирован более полвека вспять. Вначале он не получил широкого распространения из-за высочайшей цены и недостаточной надежности конструкции. Сейчас после бессчетных модернизаций и доработок аппарат заполучил гигантскую известность.
Его достоинства заключаются в последующих качествах:
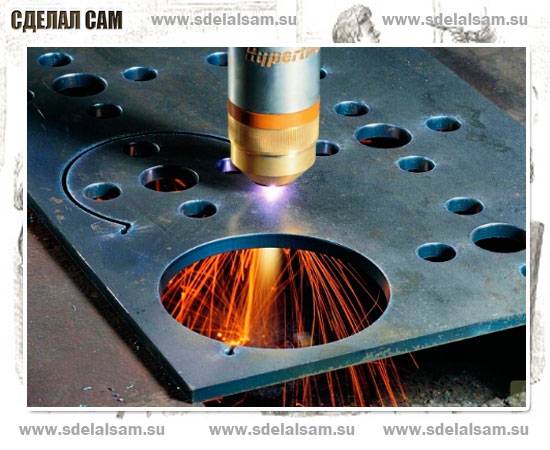
- Возможность неоднократного роста производительности – грамотный выбор мощи позволяет повысить продуктивность производства в 4-10 раз. Знатоками рекомендуется плазменная резка металла при обрабатывании заготовок, толщина которых 50-60 мм.
- Универсальность – плазморез подходит для работы с разными материалами – сталью, чугуном, железом, алюминием, титаном, медью и иными. Основное – подобрать лучший уровень мощи и подходящее давление воздуха.
- Потрясающая точность и хорошее качество – инноваторские аппараты позволяют получать идеально ровненькие края заготовок, не нуждающиеся в доп обработке.
- Высочайший уровень безопасности – оборудование является обычным и комфортным в использовании. Риск получения травм во время работы с плазморезом уменьшен к нулю при условии соблюдения правил работы с оборудованием;
- Малая степень загрязнения среды – устройство не выделяет вредных веществ. Финансовая продуктивность – плазменная резка считается более прибыльной при обработке огромных партий продукции.
Недочеты плазменной резки
Как и неважно какая другая разработка обработки металлов, плазменная резка не является совершенной. К числу главных недочетов плазмореза можно отнести последующие причины:- относительно маленькая наибольшая толщина обрабатываемых металлов – самые массивные аппараты способны совладать с заготовками менее 80-100 мм;
- высочайшие требования касаются отличия перпендикулярности – зависимо от толщины металла угол не быть может более 10-50 градусов.
является, металла, заготовок, резка, простым, плазменная, работы, регулярно, более, мощности, продукции, уровень, аппараты, задача, обработке, эффективность, которой, толщина, Резка, плазморез
Читайте также
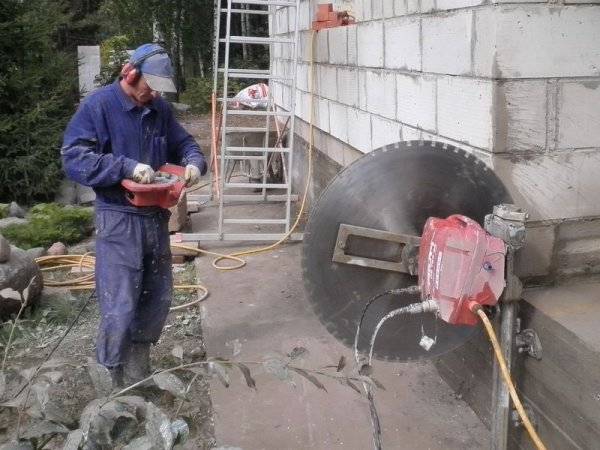
Технология алмазной резки
В строительстве набирают известность сборные конструкции из железобетона и цельный железобетон. Не имея промышленного оборудования работать с ними
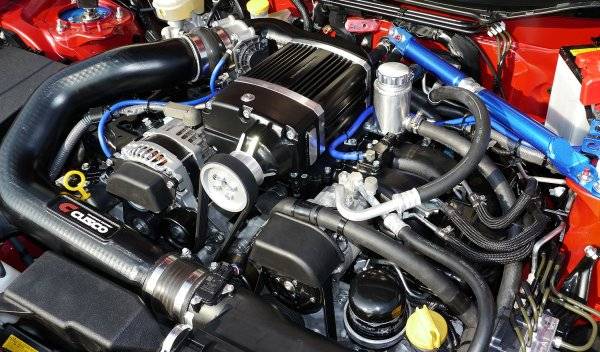
Тюнинг двигателя. Термическая эффективность и методы ее повышения
Чтоб осознать, какие способности есть для роста тепловой продуктивности мотора, необходимо правильно представлять себе, как происходит сжигание
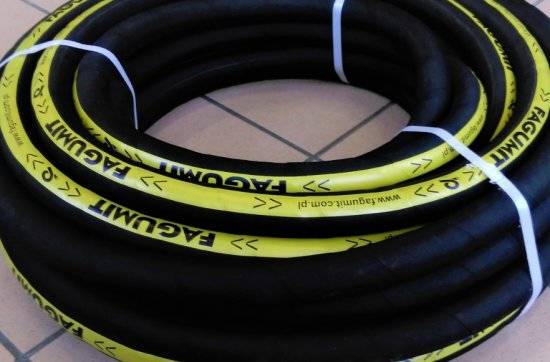
Шланг для пескоструйного аппарата: наиболее оптимальный вариант
С помощью нынешнего пескоструйного аппарата становится вероятным очистить фактически всякую поверхность от загрязнений разной степени трудности. В
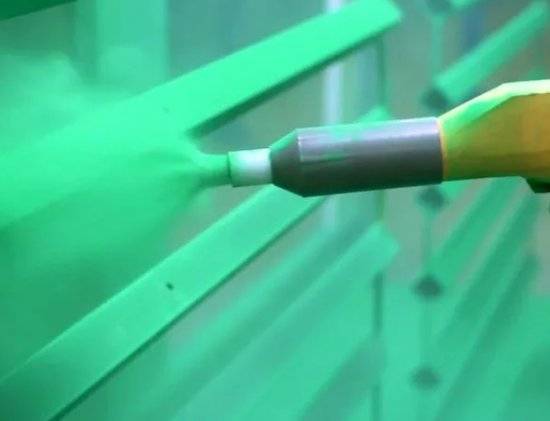
Достоинства технологии полимерной покраски металла
Полимерная порошковая покраска металла – это метод, при помощи которого можно покрывать разные железные поверхности. Она обеспечивает высшую защиту
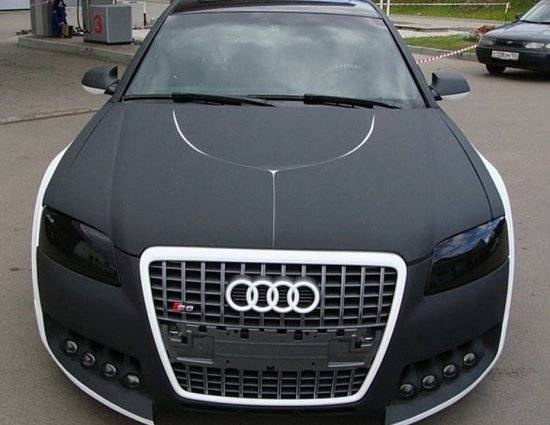
Клеим карбоновую пленку
На сегодня в мире авто тюнинга обширно всераспространено внедрение карбоновой пленки, которая является плотным материалом с текстурой похожей на